DESIGN & ENGINEERING
Wagon Tippler is used for unloading bulk carrying wagons by tipping them around an above rail level pivoted axis. Materials which can be handled are lump iron ore, iron ore fines, pellet, quartzite, limestone, minerals, etc. The above rail level pivoted side discharging tippler design enables ‘low-level” foundation work, less excavation and reduced civil-works which is the best solution for sites with high groundwater problems.

COMPLETE SYSTEMS
ISKAR’s capabilities in design, supply, installation, and commissioning provide complete turnkey wagon unloading systems includes the tippler unit, wagon holding devices, hoppers, feeders, controls and complete automation.
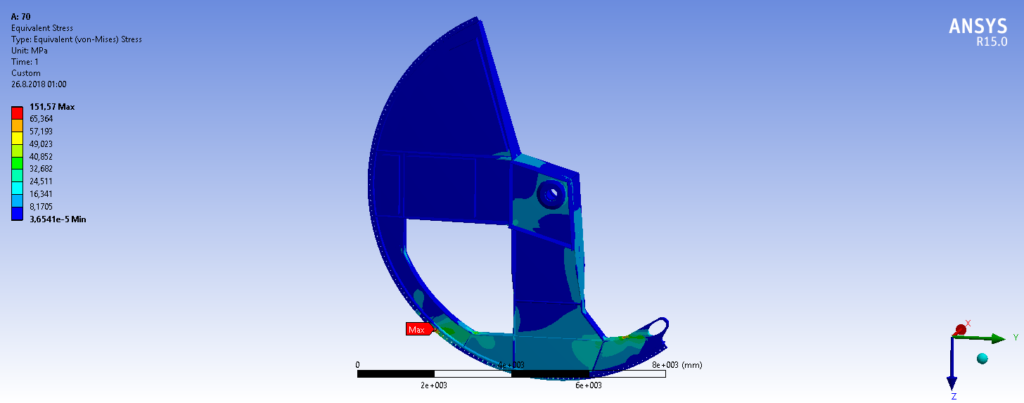
TAILOR MADE
For each individual project, the wagon unloading system is custom designed and manufactured. On a basic system configuration, the wagons are positioned on to the tippler platform by pushing them with the diesel-locomotive, however side arm positioners can be implemented depending on the requirements of the project.
ISKAR wagon tipplers secure the wagon to be tipped from top by three or four hydraulic clamping arms depending on the wagon length. The tippler drive and clamping arms are powered by a single, open loop circuit type, electric motor driven, hydraulic powerpacks unit (HPU). The Wagon Tippler is of robust construction and designed for continuous duty.

PRODUCT DEVELOPMENT
Designing wagon unloaders with state-of the art finite element analysis software allows ISKAR engineers to evaluate high stress areas prior to manufacture for secure design and optimum fatigue life.

Semi-automated systems for discharging coal and other bulk materials from open-top rail wagons, for material intake at power, steel, cement and other process plants, facilities or ports can be easily done by ISKAR wagon tipplers. ISKAR Wagon Tippler Unloading rates are between 300tph and 4,500tph.
One Wagon Tippler System consists of the following parts:
– A cradle consisting of a pair of heavy welded steel plate (end-discs) and a sector rigidly connected by a large torsion box girder fitted at each end with pivot shafts. The whole cradle is carried on pivoted shafts mounted on heavy duty spherical roller bearings.
– A rail table carried on a roller in a slotted bearing supported from an extension of the end sectors.
– Four transverse top clamp beams which are carried on arms pivoted from the main torsion box girder.
– Hydraulic drive control unit integrated on to the hydraulic power pack.
– In order to overcome sticking problem for certain materials, the top clamps can be delivered with vibration motors, to ease the free flow of the material when the wagon is at its maximum tippling angle.
– The hydraulic system and its components are so designed & selected such that the working pressure does not exceeds180 bars.
– The pivot bearings are of the antifriction type and equipped with dust seal. Adequate platforms are provided around tippler for ease of maintenance.
– Centralised grease lubrication system is provided for the tippler.
– Weighing system and dust extraction/suppression systems can be included in the delivery as an option.